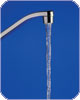
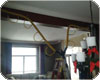
In January 2012, Austin Reisetter and his team with Rainbow International of North Central Illinois came to the rescue for a family who was not having much luck starting the New Year off right. Late at night, one of the family’s children woke up, used the sink and accidentally left it on. In the morning, the family awoke to find that pools of water had spread throughout the third story of their home. And that wasn’t all: To their horror, the water had travelled down through every floor of their home – even the basement.
Based on their insurance agent’s referral, the family called Reisetter and his Rainbow International team, and they responded by travelling over 180 miles to help. Upon arrival, he was surprised to find exotic hardwood walnut flooring completely soaked with water damage.
“This was a problem since walnut flooring is so thick and laid so tightly,” Reisetter said. “It does not open the core of the wood to accept the moisture. With oak flooring we can easily find moisture since it is much looser, making it easier to get air movement in to dry it quickly. Even the smallest amount of moisture in any wood can cause peaking and damage, making the walnut flooring our major concern.”
The family was especially distraught since the new hardwood floor had only been there for eight months and had cost over $12,000. Taking the homeowner’s concerns into consideration, Reisetter and his team began formulating a plan of action.
“For every restoration job, we meet with the customer and do a walk-through to provide a scope of the damage,” he said. “We need to find out ‘Where did the water travel?’ To figure this out, we fact-find with moisture meters to locate the moisture in the wood and try to put together a plan of action. We want as little damage as possible.”
Aside from the walnut flooring, the homeowners were worried about the livability of their home during the restoration process. The husband’s office was located in the home, and working elsewhere was not an option.
The damage was primarily in the center of the house, posing a challenge for the Rainbow International team. They needed to plan for how to strategically confine the damage, restore it as quickly as possible and still allow the family to live in their home. After serious thought and planning, Reisetter and his team devised a plan to begin their process. Focusing on the walnut flooring, the team began to use the Injectidry System to remove the moisture from the wood.
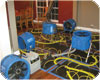
“This took a lot of focus since it is possible to leave the wood with too much moisture and have it peak, or to leave it too dry and damage it with cracks,” said Reisetter. Meanwhile, the team also tried to dry a large column with beams in the house. On the outside, it seemed to be a typical column made of sheetrock over a boxed frame, which would usually take three days to dry. They were surprised to see it was not drying as quickly as they had expected.
It didn’t take long for the team to discover that the column was not a typical column.
After opening up the sheetrock from below the baseboards (in order to cause less damage), they found that the column was made from a solid block of plywood with the sheetrock glued on, rather than the hollow box frame usually found in columns. This came as a huge surprise to the team, making the job much more complicated than originally thought.
To add salt to the wound, the insurance agent suggested that the column be completely removed. Should it have come to that, costs would be very high, and two of the rooms on the second floor of their home would need major reconstruction work. Both rooms also had sentimental painting jobs that the family absolutely did not want to be damaged. This posed a huge dilemma for Reisetter. Should they remove the column and make the insurance agent happy? Or could they discover a way to meet the customer’s desires?
The team decided to brainstorm. They called the Rainbow International home office for extra support and came to a solution.
“Instead of using the Injectidry System - which acts like a vacuum to remove the water from wood and other surfaces - we reversed the system so that it would exhaust hot dry air into the center of the column,” Reisetter explained.
The team opened up the very top of the column and used the hooks from picture frames to hold the hoses gently along the walls while the drying system blew hot dry air down the center. At the same time the column was being dried from the inside, they used machinery to dry the sheet rock from the outside. The team also placed tarps down to protect the floors from any mishaps that could occur from the column restoration.
Upon arrival, the estimated time to restore the home was about three days, which was on par with the average time required to restore homes with similar water damage. With the extra surprises from the walnut flooring and the column, the homeowners and the team were pleased to have the job finished in six days.
“The homeowners were so thankful that we found a way to avoid removing the column,” said Reisetter. “This would have been much more costly to them, and would have added a lot of extra time to the restoration process. Even the insurance agents were pleased with the results. Most other companies would have simply removed the column, regardless of the homeowner’s resistance.”
The family was very impressed and happy with the results of what started as an awful experience. They were able to escape with minimal damage to their home and with little interruption into their daily lives.