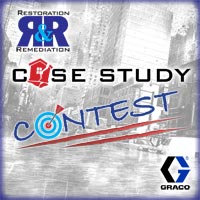
Describe this restoration project.
For several years, BrightStar Care of Madison, WI had been having trouble keeping water out of their basement. Basically, every time Madison experienced heavy rainfall, BrightStar’s basement filled with water.
In 2016 alone, BrightStar's basement had flooded twice before and was about to embark upon its third round of flooding thanks to severe storms on July 21.
A&J Specialty Services was called to the scene and began pumping and extracting water, setting up dehumidifiers and fans, performing the documentation process, and then proceeded to demo the lower 4 feet of the entire basement. After the restoration and demolition phase was complete and before we started any rebuild, the owner of the building started looking into why his building kept flooding. To prevent any future flooding to his building, the city of Madison granted BrightStar permission to reroute their sump pump drain directly to the city street.
Click here to vote!
At first, they were assuming that the sump pumps weren't able to keep up. But, as it kept happening again and again, they realized there was a much larger issue at hand. Digging deeper into the problem, it was discovered that not only were the sump pumps being routed back into a reservoir underneath the parking lot, but that the reservoir was also gathering all of the water from the parking lot and neighboring buildings. The now overflowing reservoir was forcing all of that water back through the soil, dirt, and rocks. Due to hydrostatic pressure, it pushed itself back into BrightStar's basement foundation.
Expert Thermal Engineers, Ground Engineers, Civil Engineers, and a Geological Engineer worked together to first conduct an experimental dig. They were hoping to dig a trench around the exterior of the building and fill it back in with the correct soil. It was in this experimental dig that they discovered the barrier between the holding tank and the building was either not there or improperly constructed. As a result, 1" thick steel walls were pounded 15 feet into the ground. By doing this, it was much easier to excavate and the steel walls would prevent the soil from filling in the hole.
Unfortunately, as they were pounding the steel sheets into the ground, they hit a 3” water main and caused additional flooding within the BrightStar building. When this happened, the demo had already taken place in the basement so we came back and dried it out quickly. This did cause more delays for the rebuild phase, but we persevered and overcame this and a number of other challenges, including the fact that this project required extra care as it is a Senior Living and Memory Care Facility.
What challenges did you face and how did you overcome them?
At the time this building was originally being constructed, the city of Madison required that instead of a retention pond, a retention tank of sorts would be able to absorb all of the water. It didn't.
Click here to vote!
We found out later in this project that the reservoir was constructed incorrectly and the wrong type of fill was used. In-between the building and reservoir tank, there was a patch of ground that was supposed to be left as the original earth, but it was taken out.
In this rebuild, part of problem was the outside reservoir and the soil, but the other was finding a contractor that could fix it in a timely manner. Due to the testing and legal issues with the original contractor who built the building, the rebuild was delayed by over 2 months.
The basement in BrightStar housed a full Chef's Kitchen, the Chef's Office, a breakroom, bathroom, laundry room, several storage rooms, utility room, and a server room which contained the building's electrical box.
The electrical box that supplies power to the entire building was flooded with 3 feet of water. The box itself was a 4 ft. wide by 9 ft. tall cabinet that held shelves that supplied power to various portions of the building. In order to work on the electrical box, the power to the entire building had to be shut off and the city had to pull the power from the building. And, because it was pulling so much power, the city had to shut the power down to the entire street. Once all of the power was off, the damaged panels were pulled out, the electrical box cleaned up, and new panels were installed.
The challenge here wasn’t shutting down the power, but it was actually due to BrightStar being a Senior Living and Memory Care Facility. None of the electrical work could be done during the daytime hours. Nighttime hours proved to be when the least amount of activity was occurring in the building and would cause the least amount of distractions. This meant we only had a 3 to 4 hour window of time during the night hours to get the electrical work completed. For this to happen, BrighStar's staff had to make sure residents had adequate battery packs or generator power to keep medical devices and machines running properly. The staff also had to wear headlamps while working from 2 a.m. to 5 a.m. when the power was shut off.
Another difficulty we encountered was the security measures for the residents. Being a Memory Care Facility, security is very strong to make sure the residents do not wander off. Since there were a number of outside contractors dealing with the reservoir tank and three times as many contractors, specialists, and technicians inside, special access doors were assigned and check-ins were coordinated with staff members.
Unfortunately, the majority of this project was not covered by BrightStar's Insurance Company. The owner was given a check for a very minimal portion of the loss, so ultimately it was all paid out of pocket. This project was estimated at about $370,000, which is around $80,000 less than what they had originally anticipated.
To try to save the owner money, we were able to make some rebuild suggestions and to bring in specialists to verify some of our toughest questions.
Additionally, to save time and money, we had a consultant come to verify if the VCT tile floor had to be replaced. Originally, we had thought it wasn't salvageable, but the consultant, who was also a microbiologist, confirmed that we could keep the flooring in place. This saved our client around $17,000.
We also saved money on one of the outside foundation walls. Instead of rebuilding the wall back with drywall and insulation, we chose to demo the wall completely and left the poured foundation exposed, eliminating the material cost and labor to insulate, drywall, tape and mud. This saved our client around $2,000.
This was also a rare opportunity for BrightStar to make improvements to their basement layout. Modifications to the Chef's Kitchen included adding a walk-in cooler, relocating the food storage area and Chef’s Office.
Some of these modifications were easy, but others were a bit more involved. There was a large commercial refrigerator that had to be replaced, due to the water damages, but required us to hire a specialized contractors to dismantle and cut it apart just so it could be removed from the basement. Not an easy task!
Dealing with multiple industrial kitchen appliances meant the coordination of the various contractors BrightStar was working with directly. One to deliver, one to install, one to get the correct power flowing, one to hook up all of the components, and one to...no that's it. But, it didn't stop there. An additional sprinkler head had to be installed and power rerouted to accommodate the new appliances and basement layout.