Fires, explosions, and storms were among the top causes of loss to businesses between 2013 and 2018, according to Allianz Global Corporate & Specialty’s (AGCS) 2018 “Global Claims Review. The report, which analyzed more than 470,000 insurance industry claims across the globe, revealed that 75 percent of financial losses arise from 10 causes of loss. The largest single identified cause – fire/explosion – accounted for 24 percent of the value of all claims. Other significant loss contributors included storms, accounting for 7 percent, and water damage, making up 3 percent.
When a loss due to fire, explosion or storms occurs in a business, it’s critical to return operations to normal as quickly as possible. Oftentimes, a professional restoration company is called in to assess and restore electronics, textiles and window treatments to pre-loss condition. This is because – using best practices – electronics, textiles, and window treatments are often quickly restorable at a fraction of the cost of replacement. Moreover, in many cases, restoration work can be quickly conducted on site with the goal of getting the business up and running sooner.
Through careful post-disaster assessment, tracking, and restoration, commercial electronics – everything from computers and lamps to MRI and X-ray machines – are often restorable at small fraction of the cost of replacement. Meanwhile, soft goods, including drapes, towels, bed linens and uniforms, are restorable at 20 percent of the cost of replacement. While the restoration process requires specialized training and equipment, it’s highly successful.
But, there’s no single recipe for that success. Rather, because every loss is unique, each demands a customized restoration plan that’s coordinated with and communicated to all stakeholders, including the business owner and staff, insurance provider, third-party claim administrators (TPA), any subject-matter experts and contractor.
Just how is this plan developed and executed? Very carefully …
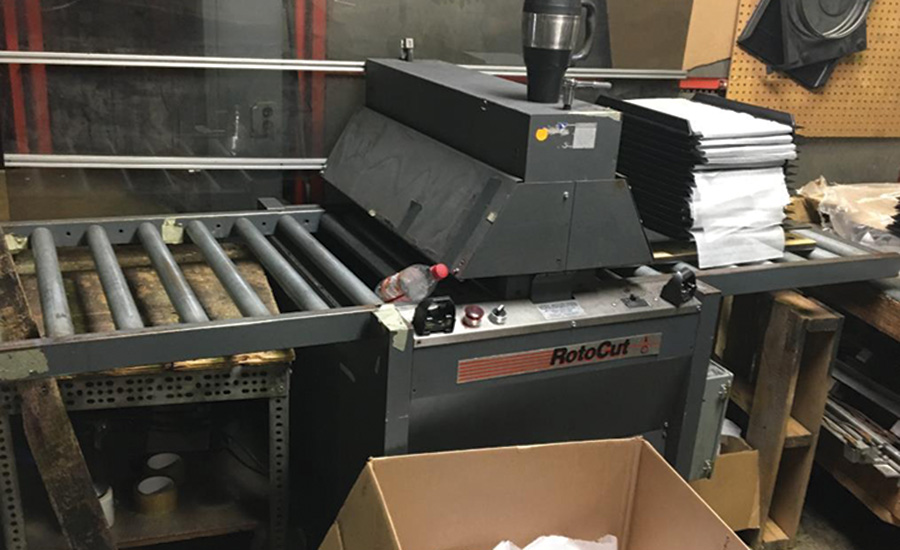
Assessing the Site
It begins and ends with clear communication. On site, at the affected business, the restoration customer service team assesses the scope of the loss while working in concert with the policyholder, insurer, key business staff, and restoration contractor. The restoration customer service team subsequently develops a plan of action for the inventory and restoration of affected items, a cost estimate, and timeline. These are quickly supplied to all the stakeholders for approval.
It’s critical that project protocols, processes, pricing and timelines are clearly established upfront and communicated throughout the restoration and claims process. While there is no exact science to this process because every loss is unique, at the core is good communication and the setting of clear expectations.
A quality restoration company will dedicate a project coordinator, or coordinators, to see the project through to completion. Once the plan of action is authorized by all stakeholders and everyone is on the same page, the restoration process begins.
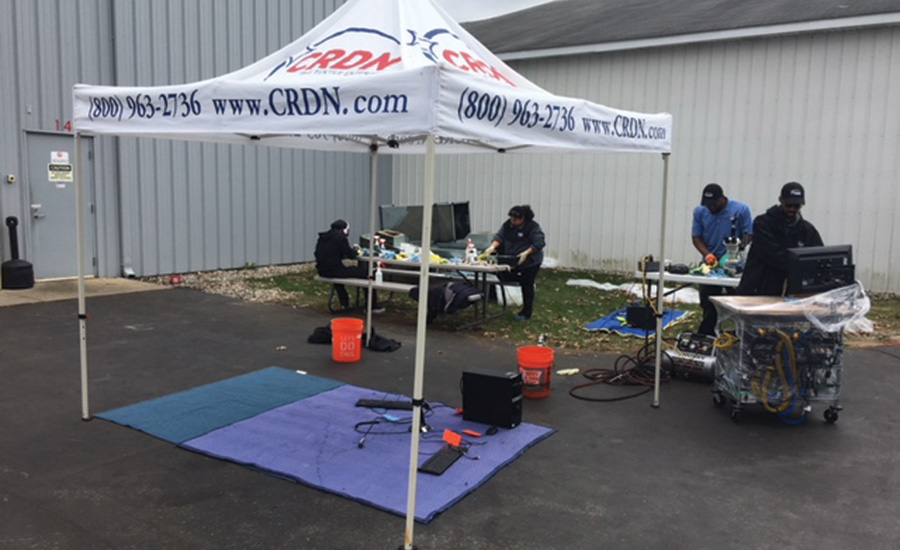
Testing, Collection, & Documentation
The first step in electronics restoration involves on site testing, where possible. Some professional firms have testing equipment or mobile carts they use to determine if a device can be restored. First, all electronics are unplugged and completely dried. Then they are powered on using the mobile testing cart. The cart allows the restoration team to test a large variety of devices, which can significantly speed up the claims process and reduce restoration costs. If they power up, generally they can be restored. If they don’t, they can’t.
In this way, the restoration customer service team can quickly determine which items were damaged as a result of the loss, helping insurance companies reduce loss liability. In the case of lightning strikes, cart testing makes it possible to see if electronics were damaged by the actual strike without removing them from the business.
In any loss where a business is impacted, it’s critical that the restoration customer service team determine where and how that company’s secure data is stored. This is usually accomplished by working in cooperation with the company’s IT director/staff.
Typically, data is stored in the cloud and/or on servers either on- or off-site. The restoration team should not come into contact with the client’s secure data, unless authorized to do so. When authorized, data transfers can be performed immediately using a number of different processes. The processes used should be agreed on by all parties.
Once authorized, cell phone and computer files can be loaded from the devices onto a memory stick and immediately handed to the IT director. Because so much content is stored on electronics – from financial documents and medical records to payroll – the restoration team needs to be thoughtful about how to access that information. It’s ideal to restore the business’ day-to-day functions by delivering data to key staff immediately.
Furthermore, anytime electronics can be restored without removing them from the property, it’s quicker, more efficient and less costly. Frequently, the restoration team can set up clean rooms or decontamination chambers, complete with necessary restoration machinery, on property. This is ideal.
If the business affected also requires textile and soft goods restoration, like a hotel, spa or casino, for example, affected bed and table linens, towels, uniforms and drapes are collected, inventoried and transported to the restoration plant for specialized cleaning.
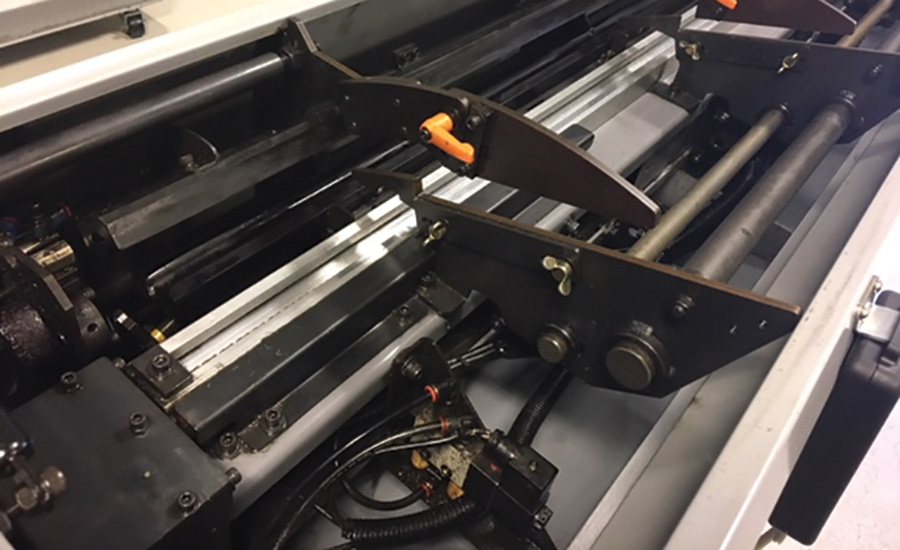
Documentation & Mapping
While onsite, the restoration team documents and photographs all the items and maps the business. Some restoration providers use proprietary technology to capture and process an inventory of items, digital images, and other documentation. The mapping ensures items are returned to exactly the same places they were found once all the company’s restoration is complete.
The Electronics & Textiles Restoration Process
Electronics and textiles are cataloged, documented and tracked. Then they undergo restoration in completely different ways.
Electronics are disassembled before cleaning. If needed, subject-matter experts are brought in to work with the restoration team on properly disassembling equipment for restoration. Electronics are then carefully restored using a four-phase process: prewash, ultrasonic cleaning, deionized water rinse, and chamber dry.
Meanwhile, textile restoration initiates with carefully drying wet items before cleaning. Best practices involve naturally drying them to prevent shrinkage using dehumidifiers, air movers, and controlled heat known as vortex drying. They are then separated for either dry cleaning or wet cleaning.
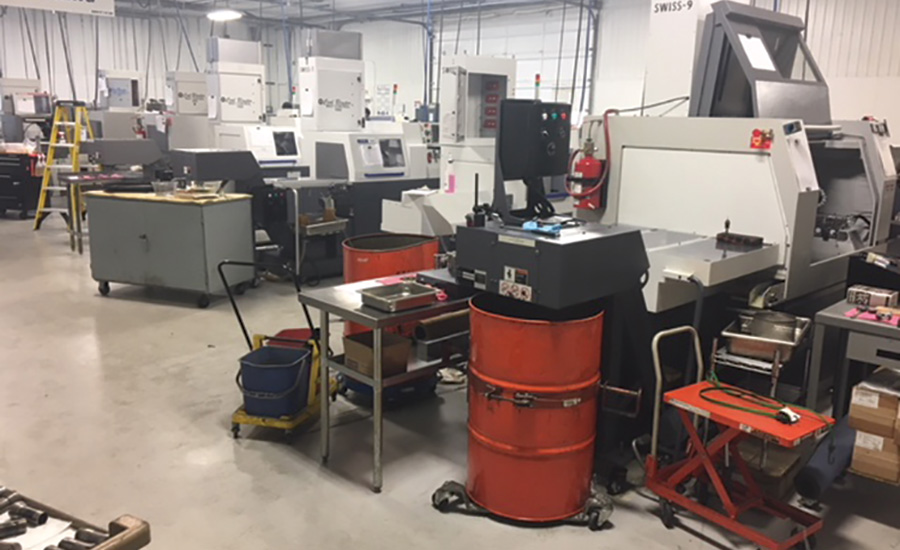
Cleaning Electronics Using Sound Waves & Cavitation
Once disassembled, electronics are submerged in a specialized tank containing chambers with separate solutions of water and cleaning or rinsing agents. This is because the safest and most thorough way to clean contaminated electronics is by using water. It’s how the military and NASA have maintained and cleaned electronics since the 1950s. It’s safe, proven and how we continue to do it today.
Inside the tank, electro-mechanical transducers produce sound waves that create millions of microscopic bubbles. As the ultrasonic bubbles form and collapse – a process called cavitation – significant heat, pressure and vacuum action combine to pull contaminants away from the device’s crevasses.
“We can’t see what the microscopic bubbles are doing,” said Lisa Morantz, president of Morantz Ultrasonics, a leading manufacturer of ultrasonic cleaning systems. “But, the pressure at the core of each bubble collapse reaches around 10,000 psi. It’s very powerful, yet very safe and gentle.” Extremely effective for removing mold and fire contaminants, the process successfully restores up to 99 percent of the collected devices, she said.
Once cleaned, electronics undergo a deionized rinse as a protective measure to prevent electrical issues as the drying process begins and to prevent spotting.
Electronics are subsequently dried inside a convection drying chamber or drying room that combines low humidity levels and constant air movement. This ensures any residual moisture is safely removed before powering the devices on again.
Following a detailed inspection, the restored items are electronically scanned and placed in secure, well-lit and humidity-controlled storage environments until the damaged business is repaired.
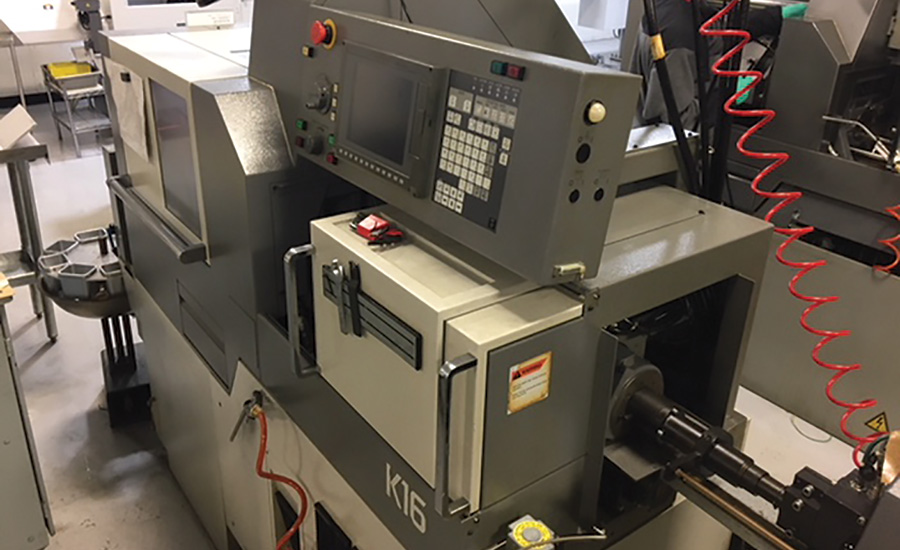
Restoring Textiles Using Dry Cleaning or Wet Cleaning
Meanwhile, the textile restoration process starts with sorting. Dry clean-only textiles are loaded into a dry cleaning machine, while the remaining textiles are loaded into wet cleaning machines. Both dry cleaning and wet cleaning are highly effective restoration processes for both water, biohazard and fire contamination.
The dry-clean only items are cleaned in a machine that uses solvents that are free of water. Thus, the term, “dry cleaning.” Some restoration companies clean dry-clean only textiles using one solvent bath. Others use two separate solvent baths. Two is better than one because after each bath, the solvent is filtered and distilled. By distilling after every bath, contaminants are not redeposited onto clothing. Finally, upon completion of cleaning processes, textiles run through an extract and dry cycle.
While some textiles require dry cleaning, a great deal are typically wet cleaned and restored using water. They are loaded into a highly programmable wet cleaning machine offering a number programs. Each program features multiple phases and automatically dictates water levels and temperatures, number of baths and rinses, cycle time, rotation/mechanical action, automatic chemical injection and extract speeds.
“Wash programs need to take into account all the factors involved in washing, including determining what additives are best for the items being processed, dosing amounts of those additives, water levels, and wash time,” said James Schulte, lead chemist at R.R. Street & Co. Inc., a leading provider of textile care cleaning chemicals.
In wet cleaning and dry cleaning, cleaning chemicals work in concert with water or solvent, water or solvent temperature, mechanical action and cycle time to significantly reduce or eliminate bacteria, viruses, and mold, as well as fire contaminants, in affected clothing.
Sometimes, textiles are also placed inside an ozone or hydroxyl chamber to further remove odors and various contaminants.
Once dry, all the textiles are steamed or pressed to produce results similar to hand-ironing. They are carefully inspected, electronically scanned, and placed into secure storage.
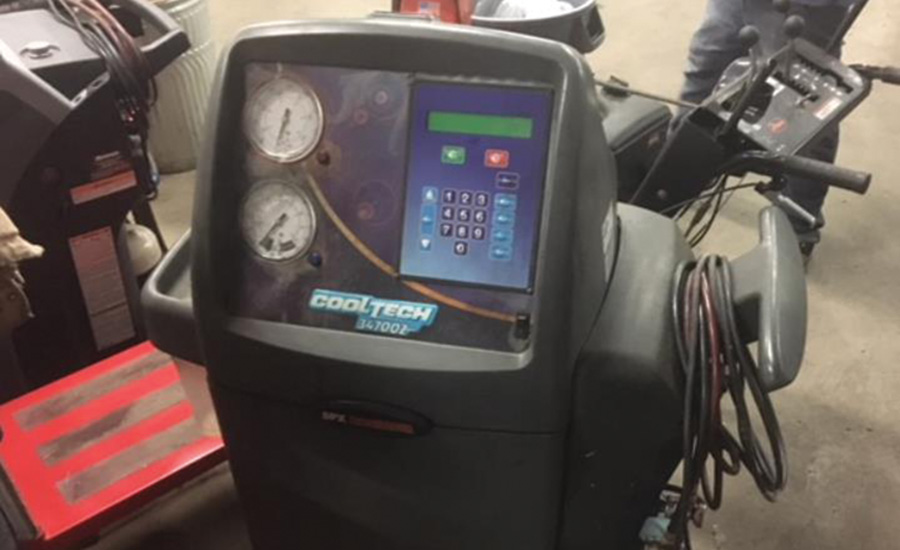
Ongoing Communication
While all this is going on, the project coordinator clearly communicates with all involved parties – the insurer, insured, contractor and TPA – to ensure a transparent and efficient process. The clear-cut plan – authorized by all stakeholders before beginning the restoration project – is carefully executed. And, at every stage in the process, the project coordinator communicates updates to the group. This keeps everyone on the same page at all times.
Such transparency is key. Restoration companies might do a great job restoring, but if they don’t do the other things – like properly scope, plan, price, and communicate the project – it can result in a disastrous outcome.
Days, weeks or months later, when the company’s repairs are concluded, the restoration team re-enters the business to re-install all restored electronics and textiles.
Convenient & Cost-Effective
While quality restoration services can return electronics and textiles to businesses at a fraction of the cost of replacement, sub-par care and communication during that process can be detrimental. When done correctly and transparently, textile and electronics restoration not only works to significantly lower claims costs and insurance premiums, it often contributes to restoring business operations more quickly. That’s a win-win for the business and insurer.
Questions? Please contact me anytime at [email protected] or visit www.crdn.com.