Editor’s Note:
This is the latest in a series of articles in R&R over the last few years on the myth of three-day drying. To see earlier articles on this topic, visit here.
While studying to become a Certified Restorer, I had the pleasure of taking a building science course offered by the Restoration Industry Association. This course should be required early in any restorer’s career. It is knowledge that will make you think differently about your drying projects.
The engineering profession has been conducting in-depth research and studying the impact of water on building assemblies for more than 30 years. Today’s restoration professionals are expected to understand how buildings are assembled and how the different building systems can impact the drying strategy. But how many restorers have a real understanding of the science behind drying a building?
Restorers have access to building science courses and I highly recommend taking one of these courses from an expert in the field. Chris Schumacher, Engineer. and Senior Building Science Specialist at RDH Building Science Inc / RDH Building Science Laboratories was my instructor. Chris explained in depth various factors and provided research that supports materials will dry with longer drying times than you would expect. He is one of the world leaders in researching and understanding building sciences and the impact of water damage on building assemblies.
Chris stresses that buildings dry at various speeds, even though the materials may be the same from one building to another.
A restorer must consider the many factors that impact drying structures. They include:
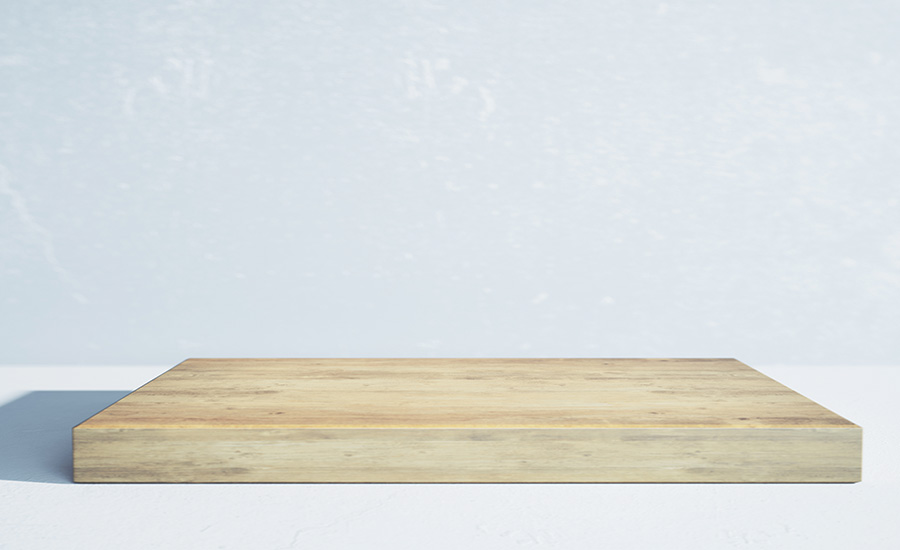
1. Material Permeance (Material Speed Limit)
Restorers use the permeance of materials to help understand how the material will respond to drying efforts. Permeance describes the material’s ability to allow moisture molecules to move through it. The higher the permeance rating, the more grains of water vapor can move through a 1 square foot material that is 1 inch thick at a vapor pressure differential of 1 inch of mercury in a one hour period of time. (Leadership In Restorative Drying, Larsen 2014).
Think of the vapor molecules as a car traveling down the highway. The car can go as fast as it wants, but the only thing hindering the speed is the speed limit. In this case, the speed limit is the permanence of the material (permissible speed) at which the moisture molecule can travel.
In a research paper from the University of Alaska, authored by Art Nash who is an Extension Energy Specialist, we can compare the permeance factor of different materials such as plain gypsum board that has a perm factor of 50 and plaster on metal lath that has a perm factor of 15 and 1 inch of concrete has a permeability factor of 3.2. Attempts to dry the gypsum board will be 3.34x faster than plaster and the gypsum board will be 15.6x faster than drying concrete. Does this maybe explain why three-day drying is not realistic or even physically possible on some jobs?
What restorers need to explain to their clients is that materials have a speed limit that can hinder the release of moisture. In some cases, you can manipulate the drying environment and create a drying strategy that will allow you to “sandwich dry” the materials, by pulling moisture from both sides of the material. You may be able to shorten the distance the water vapor has to travel because it will be moving from both sides of the material and you will be able to potentially use the faster, unfinished side of the material to accelerate your drying effort.
It is so important that restorers not only check the surface materials like drywall and carpet, but more importantly take the time to investigate the moisture levels of harder to dry materials that may be behind the surface finishes. Common materials that are overlooked by restorers are subfloor, studs, sill plates, floor joists and concrete.
2. Saturation Duration & Saturation Pressure
When a restorer considers the importance of permeance, it makes sense to consider the duration a material is exposed to moisture before the restorative process takes place. The longer a material is exposed to water, the deeper the moisture can penetrate the cell structure of the material.
Therefore, it is critical for restorers to respond to water damage losses with a sense of urgency and begin bulk water extraction as soon as practically possible. DO NOT SKIP completing your paperwork first! You have time to document the claim and get the legal ease out of the way. Then move the gear in and do your job.
Restorers must also consider the hydrostatic pressure that can be placed on a material. A material that is submerged under a foot of water will be impacted faster and deeper than a material that has water just on the surface due to the hydrostatic pressure exerted by the water on the material.
Consideration should be given to restoration efforts after a large flood caused by a storm surge, large rainstorms, or hurricanes. Materials that are submerged under a large quantity of water for an extended period can be saturated with more water and will take longer to dry.
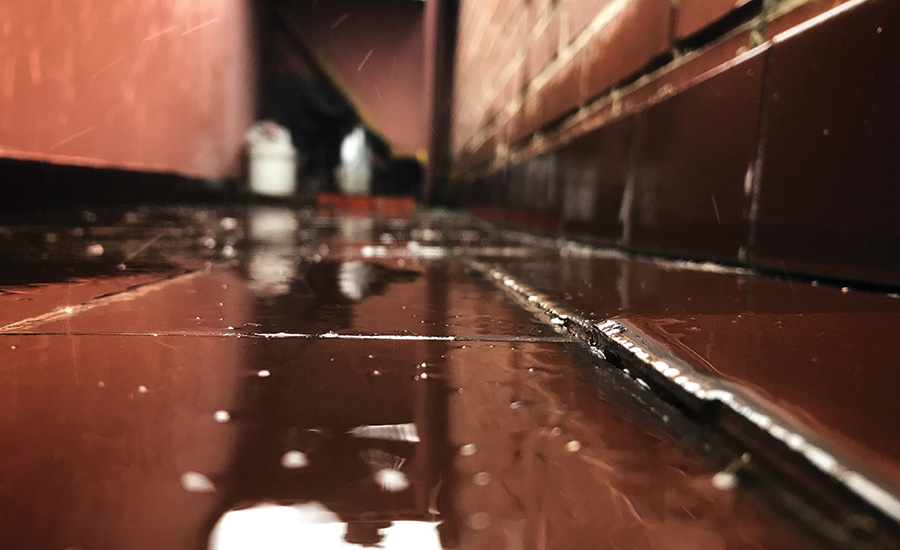
3. Building Assemblies & Building Finishes
Building assemblies are composed of various materials that on their own may respond well to drying, but when assembled can become relatively difficult to dry. There are considerations that must be given for the various vapor barriers, surface coatings and finishes that can reduce the permeance of drying materials and slow the drying process.
If you consider the normal composition of an exterior wall, you must consider the multiple materials assembled to make the wall. Drywall, vapor barrier, insulation, wood frame, and subfloor all fastened together and often sealed with tape or other adhesives. The complexity of the drying effort increases substantially when compared to an interior wall without the vapor barrier, insulation, and other similar materials. To further complicate this restoration scenario, you may encounter vinyl wallpaper, multiple layers of drywall, multiple layers of subfloor, concrete, and different masonry products. It is no surprise that restoration projects can take several days to reach the material’s dry standard in the harder to dry materials.
4. Deep Extraction
The physical removal of moisture is up to 800x more efficient compared to evaporating the same amount of moisture. While the use of wand extraction will remove as much as 20% of the water from carpet and pad, the more efficient, weighted extraction, can remove as much as 87% of the free water.
The result of removing moisture early in the process has a cascading effect for a successful water damage restoration. The restorer prevents the water from saturating the materials over a longer period of time while the restoration equipment strategy begins to work. The equipment is focused on the lower volume of moisture in the materials.
5. Vapor Pressure Differential
In order to create enough vapor pressure differential, temperatures of your drying chamber should be in the range of 85F and 90F. This provides the most efficient drying conditions for most LGR dehumidifier drying projects. These temperatures are often difficult to sustain when occupants are present in the structure. Occupants will tamper with your drying strategy and create conditions that are more suited for living in the structure. They tend to turn the heat generating equipment off (dehumidifiers) which causes the temperature to drop and so does your vapor pressure differential.
It is paramount to the drying process that the vapor pressure differential between the wet and affected materials and the drying chamber be maintained.
To put this in layman’s terms, the wet materials must have heat energy transferred to them to increase the material temperature. In return that will increase the vapor pressure of the material. The drying chamber air must remain a low vapor pressure. This vapor pressure differential is critical to effectively drying the structure.
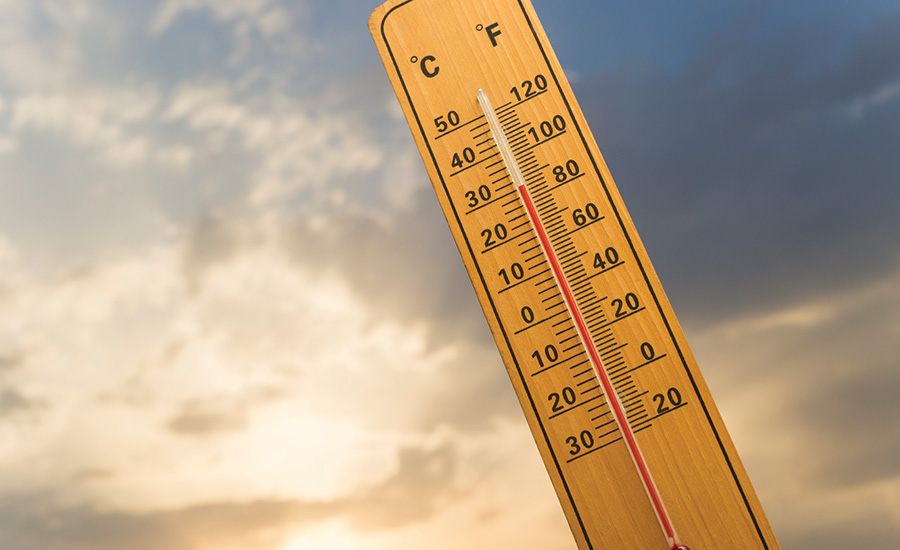
Defeating Three-Day Drying
The arbitrary use of three-day drying can be easily discounted and defeated when the job is properly documented, the readings are recorded and understood. The restorer must explain the realistic results that are anticipated and the justification for why those conclusions are drawn.
Your customer relies on your expertise and training to ensure their structure is properly dried. “Power Restorers” differentiate themselves by their level of education and ability to communicate the job with the customer; being able to communicate why a building is drying as well as the complexities, challenges and limitations that are faced daily. It is your knowledge and ability to communicate the information to your customers that will separate the Pro’s from the Joe’s!
We all want to be respected professionals within this industry, and to stand out from the crowd in whatever area of business you are focused on. You are either the company that knows what you are doing and not creating moldy buildings or you’re the company that is a revenue generator for your competition and the lawyers in your area.