Aw shucks, just slap some paint on it!” My favorite line. I have heard it several times from many people, none of whom are big in the contracting business today (thank God).

“Aw shucks, just slap some paint on it!” My favorite line. I have heard it several times from many people, none of whom are big in the contracting business today (thank God).
In the world of temporary climate control, the coatings and lining business is second to the water damage restoration industry, but a large market nonetheless. Actually, it is the part of the drying business I am originally from – the shipyards and petrochemical plants in the bayous of South Louisiana and Texas. Coatings are special products designed for very specific tasks.
Here’s another old favorite: “Ask why before you buy.”
First and always first is to identify the actual problem. Is the problem the moisture, or is the moisture a symptom of a deeper problem? Treating symptoms rarely meets with success, and quite often make the underlying problem worse. Sealing the surface of building materials may trap moisture inside them, possibly causing structural damage. So identify the moisture source first, or you might be doing this again very soon. This is truly where it all begins. Now you need to answer a few questions:
- Is the problem a one-time occurrence that has already happened (water loss, river flooding)? Drying is generally the answer over sealing.
- Is the coating for protection against a future one-time event? All you may need is a sealer for a short-term barrier, protecting the materials from getting wet.
- Is it a seasonal issue (condensation due to inadequate environmental control, elevated soil moisture levels due to rain) or a chronic situation (daily watering of gardens along the perimeter walls, low or below grade floors in a damp environment)? A higher-grade coating and prevention measures are needed if this is the case.
- Do you need to keep the moisture away from the material, as in an external coating or sealing of a below grade floor or wall? You are planning ahead of construction in this case, which is great. Look into the Portland Cement Association, which has excellent plans for contracting.
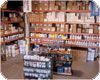
What are the conditions for satisfactory completion? Are there aesthetic values to be considered, or do we need to simply seal an unoccupied storage space? What are the different approaches available? There is usually more than one way to fix any issue; you need to explore them all. Look into both more expensive, permanent solutions and shorter-term solutions that may require rework every 3-5 years.
Keep in mind the best fix is one that will provide the appearance desired, a MTBF (Mean Time Between Failure) that is acceptable and costs that can be justified. Make sure you can deliver what the customer wants and include these criteria in the contract.
What are you coating? You need to identify the material(s) to be coated, a.k.a. the substrate(s), as there are many different types of coatings available, and usually several variations in the formulas of each type. Steel and concrete are obviously not the same, but even materials as close as poured concrete and “cinder blocks” are different enough to require a variation in the coating formulation. There are even some coatings you can apply underwater!
Once you get the above questions answered you can start the coating selection process. Remember though, there are no fix-alls. What you see in home improvement stores and TV ads may work on small spots and on a few materials only. Obtain professional advice and training from the world’s coating organizations. The best are NACE (National Association of Corrosion Engineers) and PDCA (Painting & Decoration Contractors of America); both specialize in coating testing and performance, NACE is more industrial-oriented and PDCA is more commercial building-oriented.

Of the dozen or so lining systems applied on properly dried concrete under precisely controlled environmental conditions, only two systems did not fail the test, and one was clearly superior. Only two successes out of a dozen or so of the best systems available by the largest coating manufacturers; amazing but not uncommon. Don’t select a coating solely based on the brand name; only select one by past performance of the same coating formulation on previous problems exactly like yours.
It is said that better than 85% of coating failures are due to poor surface preparation. When the label says “the surface must be clean, dry, dirt and grease free,” they mean it. That is not just a suggestion. Also, it needs to be applied in the exact fashion described, be it brush, roller, spray, etc. These application methods are not necessarily interchangeable. Go to the SSPC (The Society for Protective Coatings) and PDCA for qualified contractors to apply the system or train your people to do the job properly.
Find the real problem, establish what the acceptable results are for the customer, research the issue and finally apply the solution. You then should have a thriving green – monetarily, not microbiologically – growing business!