Sand blasting is a term long used to describe the action of blasting sand with compressed air. It’s not that simple anymore. In fact, even the name “sand blasting” is falling out of favor in many circles due to the inaccuracy of that title. The following discussion will focus on several of the changes that are occurring in the media blasting world.
The End of Sand Blasting
Media blasting is seemingly simple. Propel particles of gritty, abrasive material with compressed air against a surface to clean, de-paint, and otherwise finish it. The problem with sand blasting isn’t the blasting part, it’s the sand. Silica sand, and its associated human illness known as silicosis, has long been known to be hazardous. Crystalline Silica dust has been identified by the EPA as a human lung carcinogen. In reaction to the greater awareness of its dangers, OSHA has targeted silica sand blasting as a primary, yet preventable, source for silicosis disease. Their efforts at enforcement of current regulations, as well as new, and tighter laws, mean any contractor attempting to use silica-based media (sand) will be targeted. Being the target, or even on the radar, of this regulatory authority is not a happy place – not to mention the huge liability it creates for the business owner.
Blast Media to Fit the Application
It is easy to see why sand blasting has lost its appeal for most logical contractors. Several years ago, these savvy contractors moved away from a “sand for every application” mentality. But the switch to alternative media was not as easy as turning a valve handle on a blast unit.
Sand, as it happens, is surprisingly cheap. When you spend three to 10 times the amount for a different media, it became crystal clear that choosing the most effective, and cost efficient replacement was the new goal. Sand blasting had made media blasting itself mainstream. Now, there is new demand for the right media for the right application, instead of using sand in every instance. Today, contractors are finding walnut shell is effective and safer for taking paint off brick or wood, while maximizing the output of higher cost media. This media also minimizes damage to the substrate, a benefit that reduced the impact of the more costly materials (see picture #1).
More media has also surfaced in the marketplace – oddballs like wheat starch and sponge media. They had some niche applications like stripping aircraft frames for example, but the wide appeal and viable applications are lacking.
Some media like baking soda sounded odd at first, but had an instant appeal with the restoration and cleaning crowd. Fast, effective stripping with little, or no, damage to most building materials, and a chemical ability to deodorize soot and fire-damaged structures made it cost-effective and profitable. This example of a media-to-application coupling is still going strong to this day. (See picture #2).
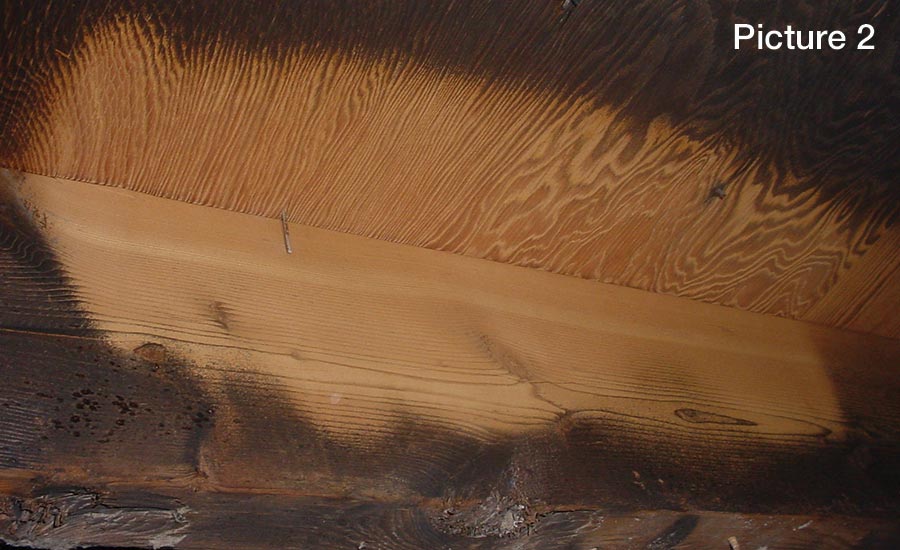
Picture #2 (Photos Courtesy of Wayne Lawrence)
Applications to Fit the Blast Media
As fate would have it, a friend called me just this morning and asked me if I recalled a demonstration we did together a short time ago. We stripped pavement marking paint off a concrete curb in an upscale and very well-maintained mobile home park. We used different dry media including baking soda, walnut shell, glass, and other crystalline silica-free alternatives. Ultimately, all of the media removed the marking paint. Some damaged the surface a little less, some a little more, but all were acceptable.
At that time, the choice of the correct medium wasn’t based on availability, or strip rate, or even the overall cost of the process. The decision was based more on the impact to the surrounding neighborhood. Since containment of the dust from the blasting was not practicable, the decision of which media to use came down to the least dust-producing method, rather than the most productive, or cost efficient.
My friend went on to question me about a similar, current application. The world’s largest online retailer is leasing properties from one of my friend’s property managers, with whom he consults on paving and concrete projects. He tells me this giant retailer has a “habit of painting everything” in the parking lots, warehouse area, and more.
“This is like the curb paint on steroids,” he exclaimed, and the next tenant “…wants it gone.”
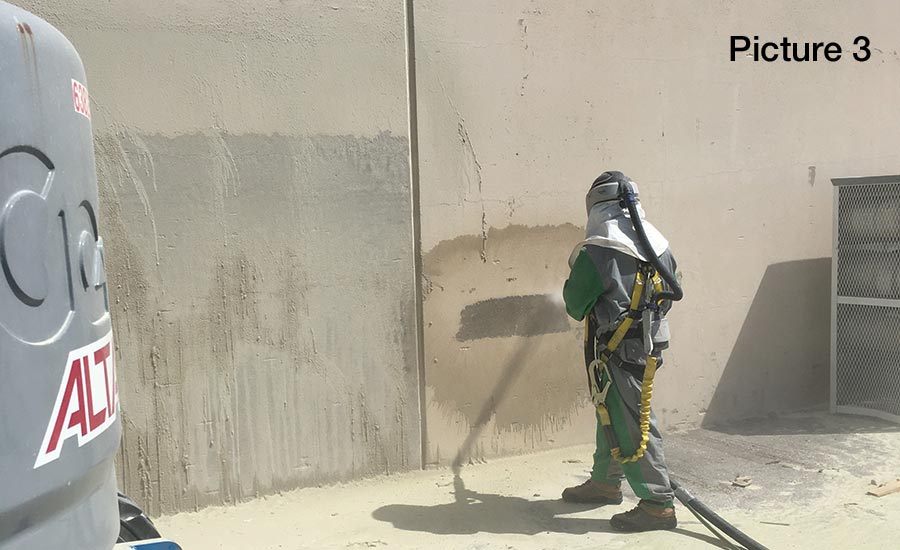
Picture #3 (Photos Courtesy of Wayne Lawrence)
Luckily, the media blasting market has also matured, and developed a process known as vapor blasting. Using a slurry of blast media mixed with water, these blast systems are virtually dustless in their application. (See picture #3) The evolution to a low or no-dust system was, of course, heralded by the popularity of dry ice blasting, but without the extremes in cost and logistics and the limitations of the medium (i.e. poor stripping ability.)
Further, unlike dry ice blasting, this vapor blasting process uses commonly-available, shelf-stable blast media like baking soda, walnut shell, crushed (recycled) glass, olivine, and garnet (See picture #4) for a wide range of cleaning and stripping applications with just a minimal amount of water – about 8 to 12 gallons per hour.
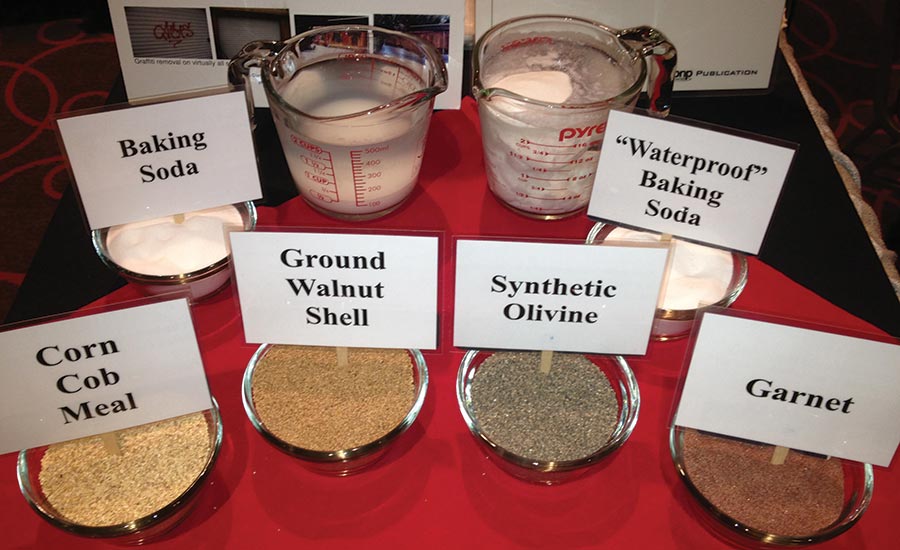
Picture #4 (Photos Courtesy of Wayne Lawrence)
A Shift in Process
A lot has changed in the blasting world over the last decade. These new trends are not complete change, not wholly new process, but a shift in the way things are applied. When the analysis is complete, however, the message is the same – using the right tool for the application is always a great idea, and ever-changing.