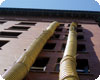
Through the years, all drying equipment, including instruments, has suffered from misinformation, or MUS (per Cliff Zlotnik, that’s all that “Made Up Stuff”). I like the equipment we employ, and even though I use all the tools of the trade, I have been labeled by more than a few as “the desiccant guy” which is as good a place to start as any.
Let’s look at the four most common myths of modern desiccants. They are:
- “Damnable to Duct”
- “Positive is the Pressure to Use”
- “Works Best when Cold” and
- “Too Expensive to Use”
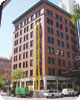
Over the last 20 years we have moved forward with flex duct, layflat and insulated HVAC ducting but clamps and connections have always proven tricky. The single best clamping method for securing duct to the unit or connections are ratcheting straps (a.k.a. cargo tie downs) from Wally World, Home Depot, auto stores, etc. They are inexpensive and much easier to acquire than the long stainless steel hose clamps we used to use.
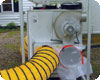
Duct work transitions through walls of a structure are much easier now than ever before. For example, Phoenix has its Easy Port, Kurt Bolden has his multi-transition Metal Duct Door. I go with these or plywood with metal collar transitions to provide a secure and weather-resistant transition in minutes.
Doorways are not always available for use, especially in occupied structures. The fire code may prevent you from blocking them, so get a commercial window installer on your subcontractor list. This is a quick and inexpensive way to make the transition if the windows do not open.
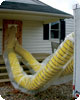
Ducting only the reactivation air out will generally result in a negative pressure environment. This will cause air outside the affected area to infiltrate. Be careful: if grains are high or the temperature is undesirable outside the affected area, the amount of this infiltration may make it really difficult to reach the really low grains desiccants are famous for, adversely affecting your drying time.
You may want to run a “reactivation air in” duct to bring the affected area to a neutral pressure (recirculation of reactivation air). Remember to always control your ingress and, on high-end homes or commercial projects, consult with an HVAC engineer to ensure no environmental or safety systems shall be adversely affected.
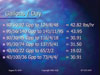
Recirculation or neutral pressure will generally produce the lowest grain level because you are removing moisture with every pass through the desiccant; as the building grains drop, so will your process-out grains. This occurs over and over until grains bottom out, usually in the teens or 20s with a purge or low reactivation temperature desiccant (which are difficult to over-dry with), and into the single digits with at standard or 4-hole desiccant.
Extra myth dispelled here: desiccants don’t split wood; people who do not monitor their drying progress split wood!
My personal favorite myth, and the most repeated, is that desiccants don’t like hot air, or that they don’t even dry when it is hot. Well this is BS, not just MUS. The proof is in the numbers in Table 1.
The table shows the Temperature/Relative Humidity/GPP in and then out, equaling pounds of moisture per hour removed. Notice that 400F/100 RH is the same water removal as 950F/30 RH. The air temperature is more than twice as hot and the unit is still drying well. Busted! I believe this myth started long ago with lithium chloride rotors that were far more temperature sensitive. The silica-gel units we use today should work well into the 110-1,200F range.
A great benefit of desiccants is that they produce heat as a by-product. If you want higher air temperature to raise the material temperature (increasing the material’s vapor pressure) while maintaining the lowest air vapor pressure possible, the desiccant achieves both. But keep in mind that contents (wine, candles. chocolates, etc) and people have a temperature limit (and sprinkler heads: never, never forget the sprinkler heads), so spot heating might be the best overall choice for heating stubborn materials.
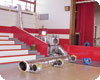
- On a 3,000-5,000-square-foot loss, you would need either 3-to-5 LGRs or a 900 CFM desiccant.
- A 900 CFM desiccant at $550/day x 3 days = $1,650
- Five LGRs at $125/day x 3 days = $1,875
Commercial projects are where desiccants shine, as long as you have access to larger areas:
- One large 5,000 CFM at $1,500/day x 3 days = $4,500.
- 24 LGRs at $125/day x 3 days = $9,000.
- Even if you add in generator and fuel, the desiccant costs less.
I hope you have a better understanding of desiccants, have gained a few extra usage tips, and realize that no one knows everything about everything. I wish you profitable drying.